What is an RI&E and when is it mandatory?
As an employer, you want your employees to stay healthy and vital. In this you also have a responsibility, which is defined in the Working Conditions Act (Arbowet). The Risk Inventory and Evaluation (RI&E) is part of the Working Conditions Act. With an RI&E you identify all the risks within your company. Once you have done that, you can take measures and actions to eliminate or at least reduce those risks.
Legal obligation
An RI&E is mandatory for every company in every industry that has one or more employees. If you have more than 25 employees, you must have your RI&E reviewed by a certified occupational health and safety service or occupational health and safety expert. There is one exception to this rule: if you make your RI&E with a recognized sector instrument, this review is not necessary. You can find lots of useful information about everything concerning the RI&E via the RI&E Support Centre.
Appropriate to the work situation
Not every RI&E is the same, and that makes sense. After all, the risk profile of an accounting firm is different from that of a construction company. That's why you can make an RI&E that fits your company's work situation. A fixed part of the RI&E is the plan of action, which contains the measures you are going to take to deal with the inventoried risks. Making an RI&E is not difficult, but it does take some time.
How do you get the RI&E under control?
Having an RI&E is one thing, managing an RI&E is "a completely different story. Once you have mapped out your business risks, you naturally want to evaluate them and see how you can reduce or control those risks so that they are brought to an acceptable level.
But what is acceptable? How do you link control measures to the risks you have inventoried? Who do you make responsible for which control measure? How do you check whether that responsibility is taken up? How do you know whether management measures have been implemented? What is the residual risk remaining after implementation per management aspect? How does that residual risk develop over time?
A little quality/risk manager must be able to give concrete answers to those questions. Then it's nice if you can bring all those aspects under control with handy and complete software. For that, take a look at the RI&E component in the ISO2HANDLE platform.
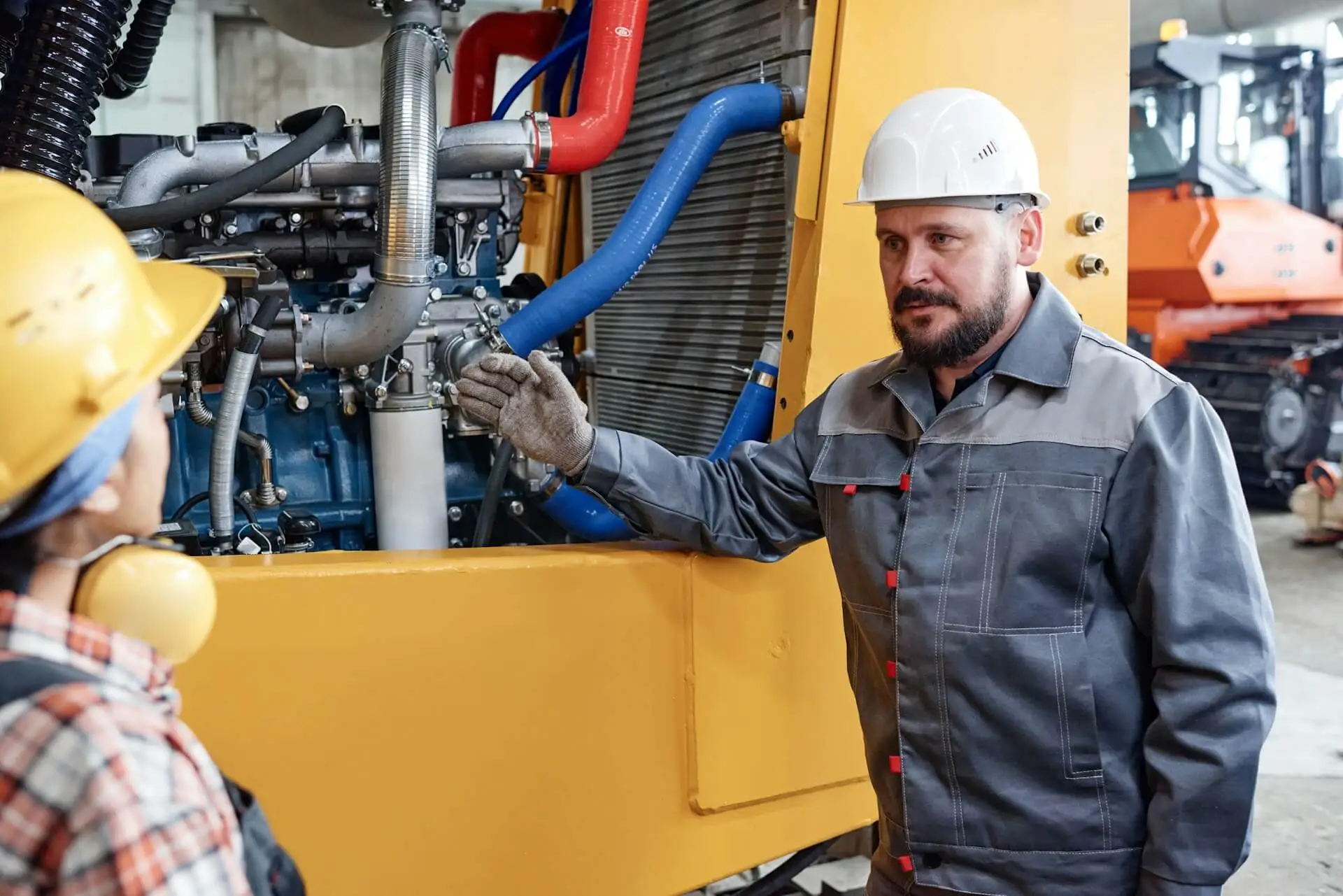
10 Tips to make the risk assessment and evaluation live on the shop floor
If, after compiling your RI&E, you move on to the order of the day, that's a missed opportunity. After all, you make such an approach for a reason. Therefore, we would like to give you inspiration with 10 tips to make your RI&E come alive in your company.
Tip 1: Actively engage employees
To begin with, it is already a good idea to involve your employees in the creation of your RI&E. They themselves have a good idea of the risks they run in their work. Besides that substantive argument, making or maintaining an RI&E also sends a positive signal to your employees. It shows that you take their health and vitality seriously and that you value their input in making or maintaining the RI&E.
In practical terms, you can think of shop floor interviews, in which you ask employees for their input on safety and risks. You could also form a working group responsible for maintaining and implementing the RI&E. That working group could, for example, have a permanent core, with a flexible shell of changing employees. For optimal acceptance, it is advisable to have managers and employees participate in such a working group. It is also important that employees can report risks via a central hotline.
You could use the notifications component of your ISO2HANDLE platform for this. If you use an intranet for this (e.g. Sharepoint) you could easily link it with ISO2HANDLE. What your employees enter via Sharepoint then enters your digital quality management system directly. This is very convenient because you can follow up on reports automatically from that environment. You don't have to do that manually.
Tip 2: Make your RI&E practical and visible
Visibility is important for acceptance, because an RI&E that is gathering dust in a drawer will not easily catch the eye of your people. Therefore, use posters, infographics, videos and publications on your intranet to draw attention to safe and healthy working. For each publication, you can focus on the most important themes and points from your RI&E.
You can also organize practical exercises and simulations. For example, you can teach your employees how to act in a dangerous situation. If they have practiced a few times, they will be better able to act in real life situations.
Separately, you can integrate safety rules into daily briefings, newsletters, team meetings or start work calls.
Tip 3: Perform continuous monitoring and updates
In many work environments it is normal to do inspection rounds from time to time. You can easily combine these with safety rounds, so you and employees look at the workplace in more ways at once.
Of course, you can also do your inspection rounds and safety rounds (separate or combined) via your smartphone on ISO2HANDLE. Add the input from the shop floor to the RI&E and thus show that comments are taken seriously.
Tip 4: Make safety part of company culture
Executives should lead by example by strictly following safety rules and proactively helping colleagues do the same. This is something you can discuss in your MT so that workplace safety gets broad support from company leaders. Work to create a culture where there is open communication.
The goal should be that employees feel safe to report risks or problems without fear of repercussions. Reward colleagues who identify risks and suggest improvements with a compliment or small token of appreciation. This emphasizes that you value their input, which encourages others to actively participate as well.
Tip 5: Evaluate and continuously improve
Schedule review sessions with employees about the effectiveness and timeliness of RI&E actions from the action plan. These moments of reflection give you the opportunity to keep your RI&E up to date and at the same time draw attention to it.
Analyze incidents and near misses and incorporate the lessons learned directly into your RI&E. Meanwhile, of course, you check whether your RI&E is still in line with current processes, new machines and adapted laws and regulations.
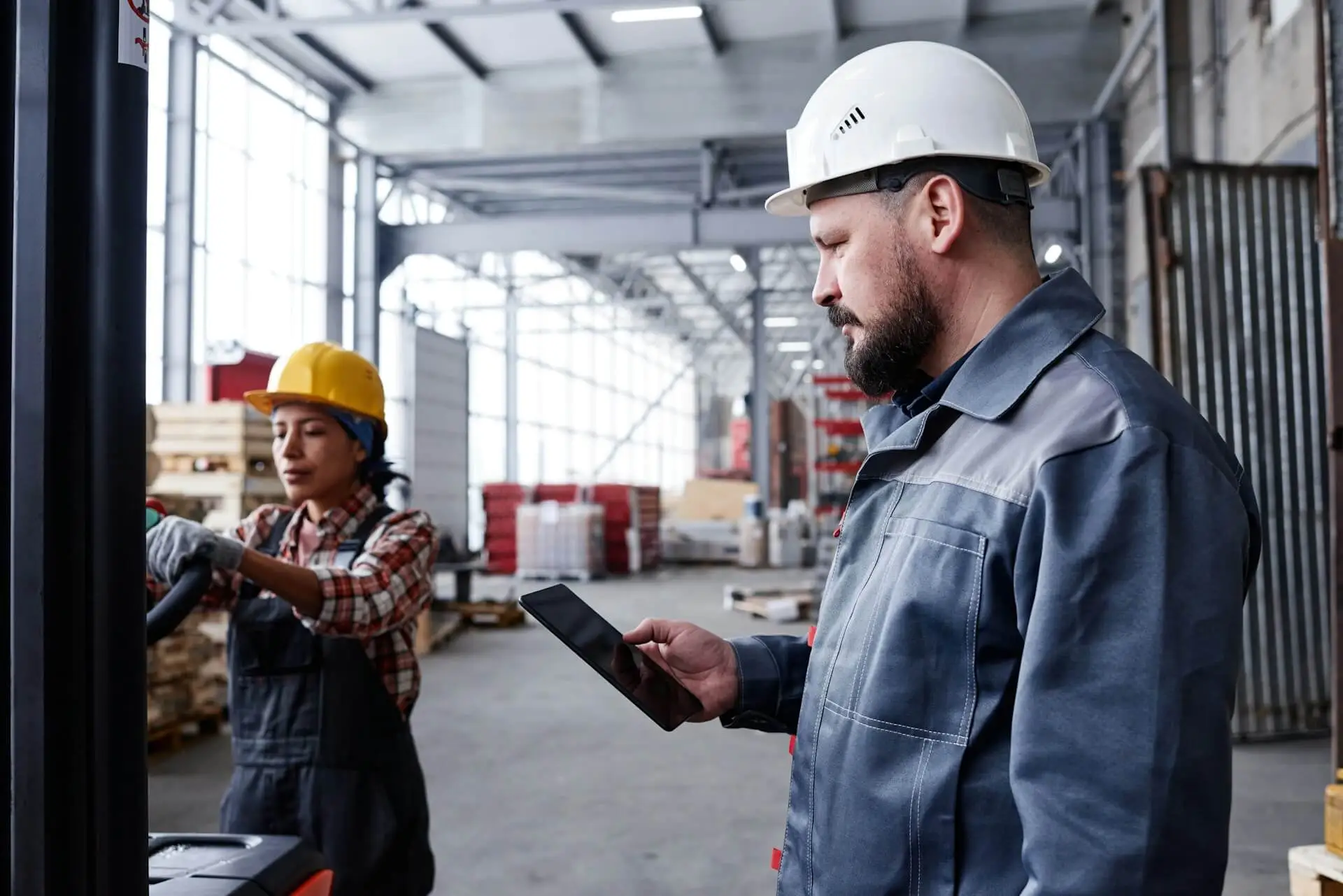
Tip 6: Provide engaging and interactive training sessions
Your employees are obviously not going to study and memorize safety instructions and procedures. If you want them to work more safely, it's better to have them practice with real scenarios that may occur in their workplace.
To make it fun, you can still translate those scenarios into interactive games, quizzes or challenges. Gamification is what we call it, and it works very well. It's smart, though, to create short moments of attention to safety on a regular basis. That's better than one long training session a year.
Tip 7: Link RI&E to practice.
You can very well discuss safety during a team meeting and start or end meeting, where projects are involved. At a start-of-work meeting in the construction industry, safety is often a fixed part of the discussion. At such times you can also demonstrate how action points from the RI&E can contribute directly to reducing incidents.
Also communicate regularly about the results achieved. For example, that your company has been operating without accidents for x months.
Tip 8: Create a sense of ownership
Without a problem owner, nothing is going to happen. That is why it is good to assign specific action points from the RI&E to employees or teams. It is important that those responsible also have a certain degree of autonomy. They themselves must be able to work on solutions to risks in their workplace. After all, they themselves are the best experience experts you can think of. And if your employees then come up with input, show them how that input is incorporated into the RI&E and what the results are.
Tip 9: Organize safety campaigns and events
To bring or keep attention to safe working you could organize an annual theme week in which extra attention is paid to risks and prevention. During this Safety Week you can invite experts or experts by experience to speak about safety. To keep the subject alive, you can also think of another form of gamification. If you can put safety into a score, organize a safety competition. That way you can have teams compete against each other for a monthly or annual reward. You don't have to immediately think of large gifts or amounts. A reward can also be intangible or symbolic.
Tip 10: Make it a PDCA cycle
Organize your control measures in a PDCA cycle. Then you ensure that they are always up to date and relevant. That gives you an RI&E that is in good condition at all times. It does not contain any superfluous or less relevant control measures and thus remains an active and manageable instrument.
How do you make your work more effective with good RI&E software?
Je leven wordt wel een stuk gemakkelijker als je goede RI&E software gebruikt.Het helpt je om RI&E vragen in vraagdomeinen te organiseren. Je koppelt eenvoudig automatische workflows en taken aan vragen die actie behoeven. Je ziet direct welke taken nog niet zijn opgepakt of afgerond en automatische notificaties helpen je in de opvolging. Je gebruikt je RI&E dashboard in combinatie met je andere QHSE/KAM dashboards voor compleet overzicht en optimale controle. Deze functionaliteit en nog veel meer vind je in het ISO2HANDLE platform.
If you are interested in seeing this in more detail - for example, via an online demo - please contact us.
Meer lezen over de RI&E in de praktijk? Bekijk dan eens ons recente artikel: RI&E voorbeeld: Zo stel je een effectieve RI&E op