What is an Risk inventory and Evaluation (RI&E) and why is it important?
Nice one RI&E, but how do you set it up? Where do you start and what makes the difference between minimal compliance and truly effective RI&E? In this blog, we'll give you practical RI&E examples and show you how smart software can make the process easier and more efficient.
One RI&E (Risk Inventory and Evaluation) is a method for identifying risks in the workplace. Under the Working Conditions Act, every company with staff is obliged to carry out an RI&E, regardless of the sector.
What does an RI&E have to comply with?
A good RI&E always includes three parts:
- It must identify the risks present.
- An assessment of the seriousness of these risks, including possible consequences
- It must include an action plan with measures to reduce the risks.
Who is responsible?
The ultimate responsibility lies with the employer. In practice, execution is often delegated to a QHSE or KAM manager. They ensure that the RI&E is up to date. They must also ensure that the RI&E is tested and assessed by a certified health and safety expert.
How do you set up a good RI&E?
An RI&E should not only be up to date, it must also contain the following three essential components:
1. Risk inventory:
here you identify all potential hazards in the workplace. Think about:
- Physical risks: such as the risk of falling, noise, or exposure to hazardous substances
- Psychosocial risks, such as work pressure, stress, aggression or unwanted behavior.
2. Risk assessment:
Not every risk is equally serious. During the evaluation, you will assess:
- What is the chance that the risk will occur?
- What are the possible consequences?
This assessment helps you set priorities: which risks require action at the moment, and which ones can be addressed later?
3. Action plan:
based on the evaluation, you will draw up a concrete measure. A good plan of action states:
- Who is responsible
- What needs to be done
- When it is executed,
- How progress is monitored
A good plan of action meets the SMART: specific, measurable, acceptable, realistic and time-bound.
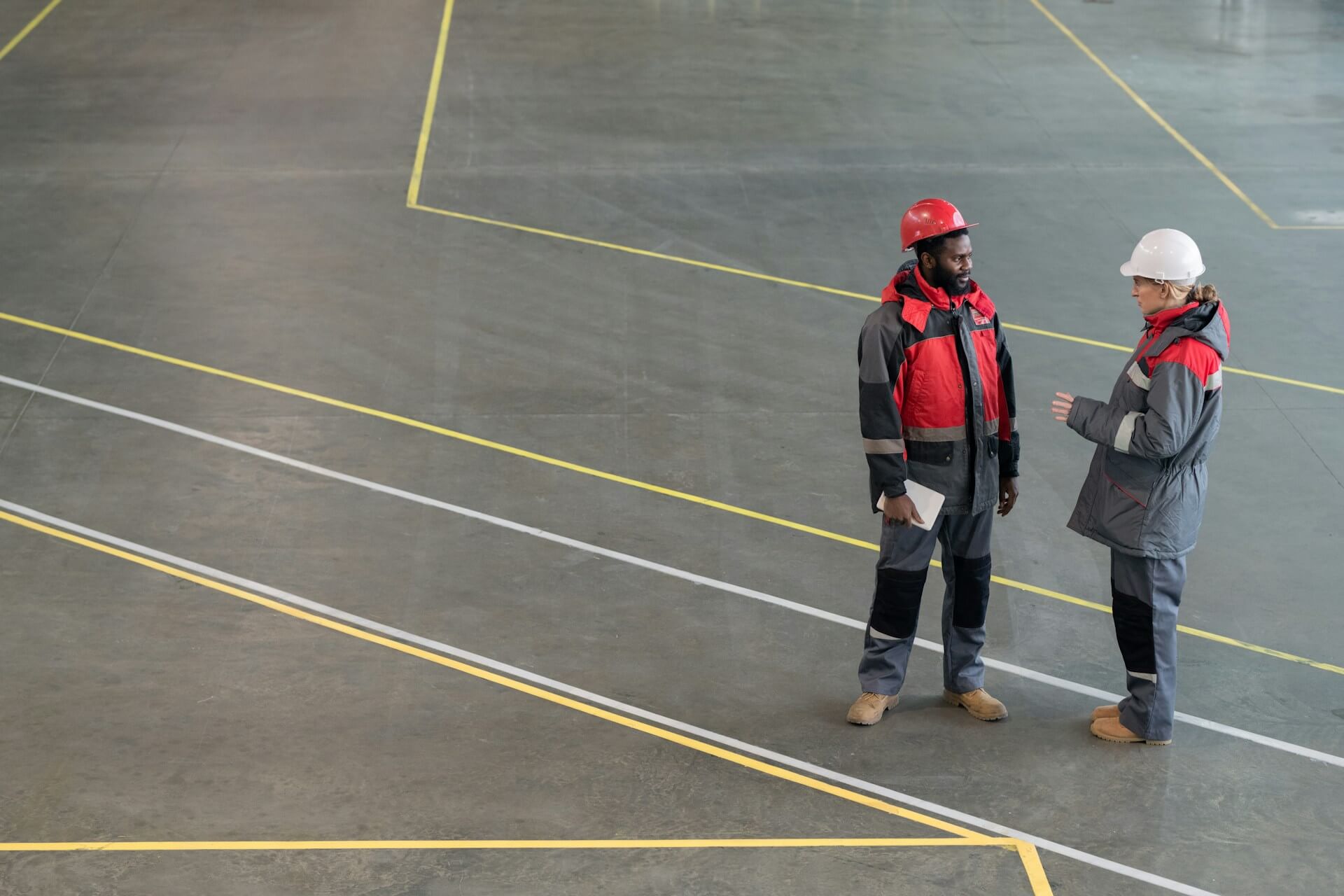
RI&E Practical examples
Are you looking for an example for setting up a good RI&E? Then you're in the right place. We would like to give you three practical examples and explain how to draw up a risk inventory.
1. RI&E example construction
Present risks: risk of falling when working at heights, exposure to noise (machines, tools) and incorrect use of personal protective equipment (PPE).
RI&E action plan:
- Mandatory fall protection when working above 2.5 meters.
- Carrying out noise measurements and providing employees with hearing protection.
- Stricter control over the use of PPE and provide safety training.
2. RI&E example metal and technology
Present risks: the risk of cutting caused by sharp materials and machines, exposure to hazardous substances and dust, and accidents caused by unprotected machines.
RI&E action plan:
- Mandatory use of cut-resistant gloves.
- Improving the extraction systems and having employees regularly undergo medical examinations.
- Improving machine protection and tightening maintenance protocols.
2. RI&E example transport
Presence risks: traffic accidents due to time pressure and fatigue, physical strain due to heavy lifting and dangerous traffic situations when loading and unloading.
RI&E action plan:
- Compliance with strict rest periods and time trial monitoring systems.
- Providing training courses on ergonomic lifting and using aids.
- Optimise traffic routes on business premises and mark them more clearly.
Common mistakes at an RI&E
Setting up an RI&E correctly requires involvement and analytical skills. Unfortunately, companies still often go wrong in setting up an RI&E correctly. These are the four most common pitfalls for companies, take advantage of them and don't fall into the same pitfalls:
- No current RI&E: an RI&E must always remain a living document. When work processes or risks change, this will have to be updated in the RI&E.
- The absence of an action plan: if a concrete plan of action is missing for your RI&E, it remains an aimless paper document. You must ensure that the measures taken are actually implemented.
- Employee engagement: The employees within your organization know better than anyone what the possible risks of their workplace are. Actively involve your employees in setting up the RI&E to ensure compliance with the RI&E. See also our article: 10 Tips for Making the RI&E Live in the Workplace.
- RI&E assessment: does your organization have more than twenty-five employees? Then the RI&E must be tested by a certified health and safety expert, don't forget! It prevents omissions and increases effectiveness.
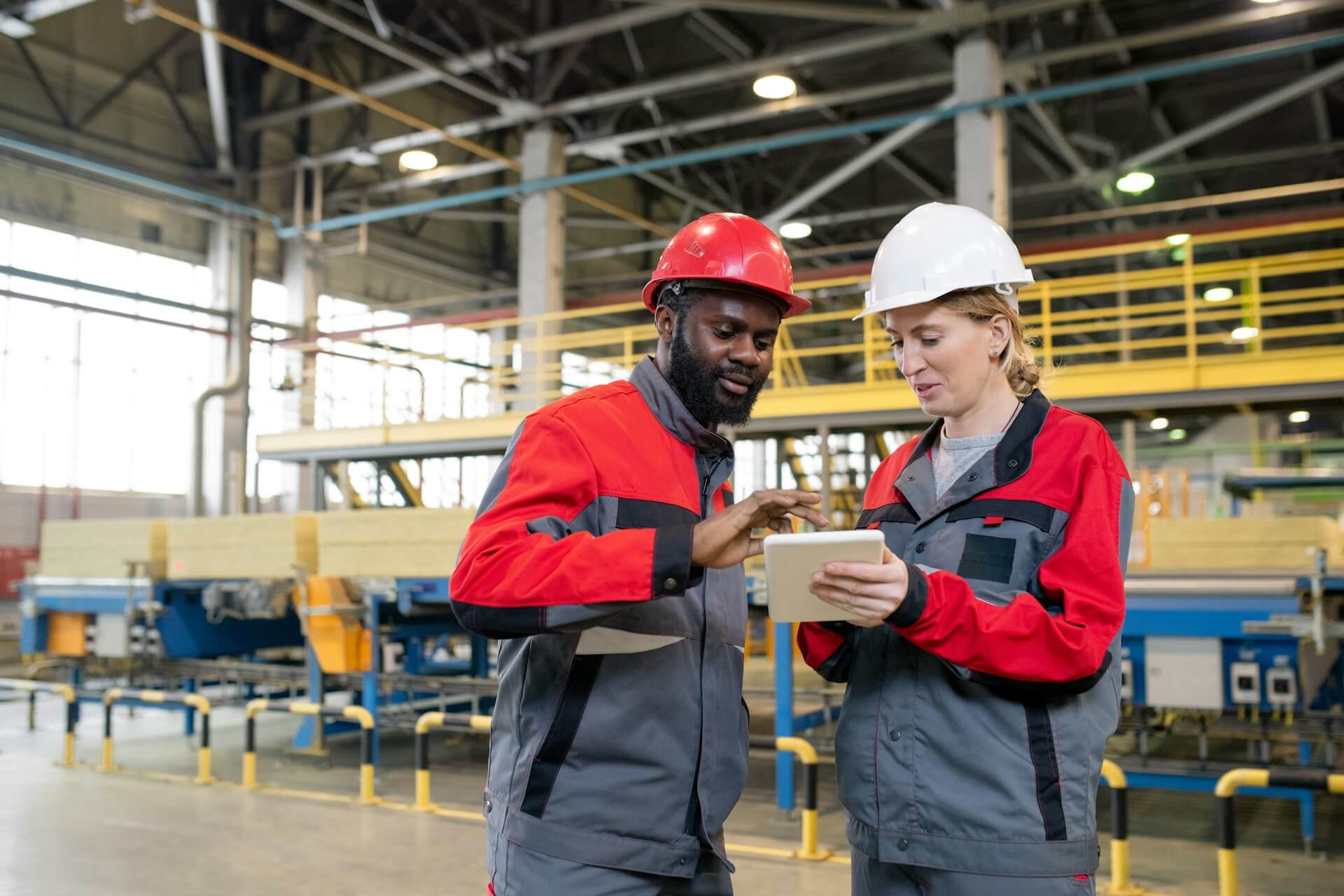
How do you make your work more effective with good RI&E software?
Your life does get a lot easier when your good ones RI&E software used.It helps you to RI&E organizing questions into question domains. You can easily link automated workflows and tasks to questions that need action. You can immediately see which tasks have not yet been completed or completed and automatic notifications help you follow up. You use your RI&E dashboard in combination with your other QHSE/KAM dashboards for a complete overview and optimal control. You can find this functionality and much more in the ISO2HANDLE platform.
Conclusion
One RI&E is an essential tool for providing insight into occupational risks in the workplace and also reducing them. Due to the legal obligation, safety in the workplace is thus guaranteed. By avoiding common pitfalls and using our smart software, you can create a RI&E organize more efficiently and effectively.
Are you interested in taking a closer look at this - for example via a online demo - then take contact with us.
Quality, Health, Safety and Environment?